Je suis une personne impatiente et, en tant que telle, j’ai hâte que le lit (fourni d’origine) de mon imprimante atteigne les températures PETG. Un lit de 300x300mm, une journée froide, prendra un temps considérable pour atteindre 70C. J’ai donc mis un lit 220v (tension secteur là où j’habite).
Le représentant français (local pour moi) de Tenlog StudioLab 39 propose cela en tant que service, vous pouvez acheter l’imprimante avec le nouveau lit installé ou un kit. Si vous ne vous sentez pas à l’aise de mettre vos doigts à proximité de la tension secteur, je vous conseille fortement de trouver votre revendeur local et de demander que cela soit fait par un expert. De plus, ceci est un compte rendu sur la façon dont je l’ai fait et, en aucun cas, un conseil pour le faire vous-même.
J’ai acquis les pièces via aliexpress (la plupart d’entre elles étaient disponibles auprès de revendeurs locaux mais ils proposaient les mêmes articles moyennant un supplément), j’ai basé ma liste d’achat sur ce que le revendeur officiel proposait et quelques autres sources sur cette modification, voici le plein BOM (certains de ces articles que j’avais déjà):
-
Le element chauffant:
-
Le relay (attention, cette pièce peut être contrefaite, préférez celles d’origine locale dans des magasins réputés, ce n’est pas important pour moi mais votre kilométrage peut varier):
-
Un fusible thermique:
-
Une prise décente pour pouvoir déconnecter notre lit facilement:
-
Un moyen de mettre un fusible entre le secteur et l’élément chauffant:
- J’avais aussi besoin de fusibles, mais j’avais ceux en stock pour l’imprimante, j’ai fait correspondre le même fusible que celui utilisé par l’alimentation de l’imprimante:
-
Si votre modèle n’a pas de connecteur pour le lit (le câble va directement dans le boîtier), vous en aurez également besoin de ca:
-
Pinces à sertir et bornes pour le secteur et autres bornes de puissance:
-
Pince à sertir pour connecteurs DuPont/JST:
-
Gaine thermorétractable. L’isolation, les pièces mobiles et la tension secteur nécessitent un blindage supplémentaire:
- Un fer à souder puissant:
J’ai également reçu beaucoup de bonnes idées et de consignes de sécurité de la chaîne youtube TeachingTech:
La section de téléchargement de StudioLab 39 STL fournit également des informations utiles. Les STL disponibles sont obsolètes et très probablement le seul qui conviendra à votre machine (si vous avez l’un des nouveaux modèles) est la boîte à relais.
Tout d’abord, j’ai cherché une grande surface pour travailler. J’ai réquisitionné la table de la salle à manger de ma maison.
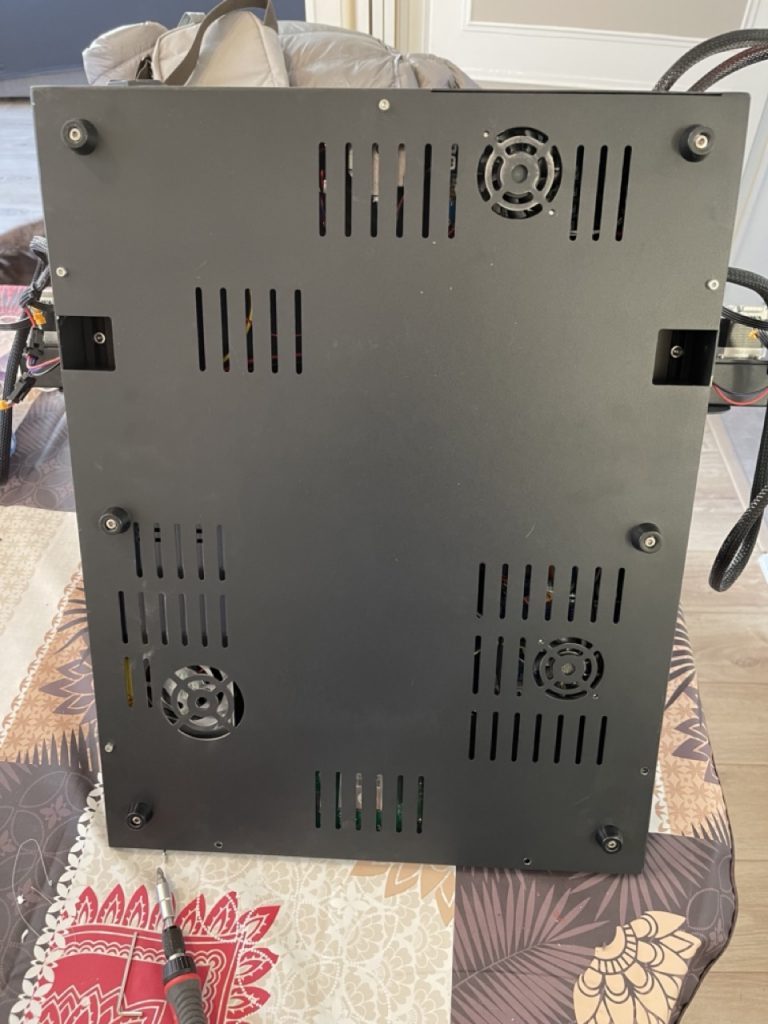
Retirez le couvercle, il y a pas mal de vis. J’ai profité de cette occasion pour mettre également à niveau les ventilateurs vers Sunon Maglevs et remplacer le bloc d’alimentation (j’en utilisais un de rechange parce que le mien avait besoin de remplacer certains capuchons, ceux d’origine sont sous-spécifiés et finissent par abandonner).
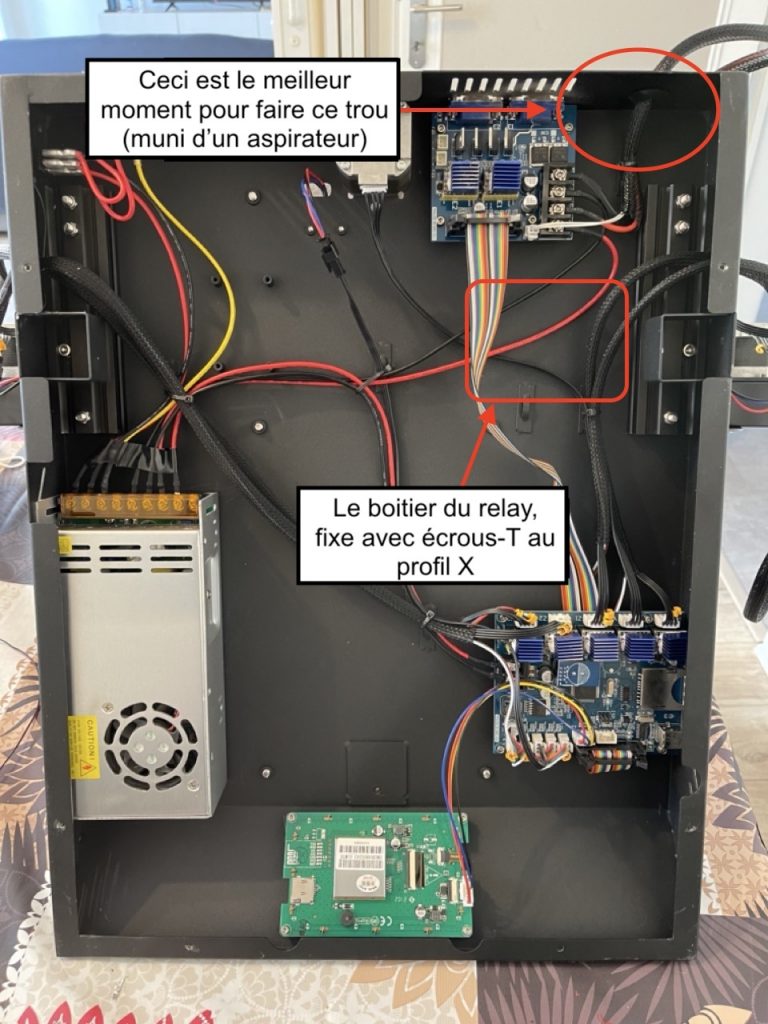
La majeure partie de votre attention doit être fixée sur le plateau supérieur. Je pense que les pilotes là-dedans sont ceux de l’extrudeuse, il contient également le circuit de chauffage du lit.
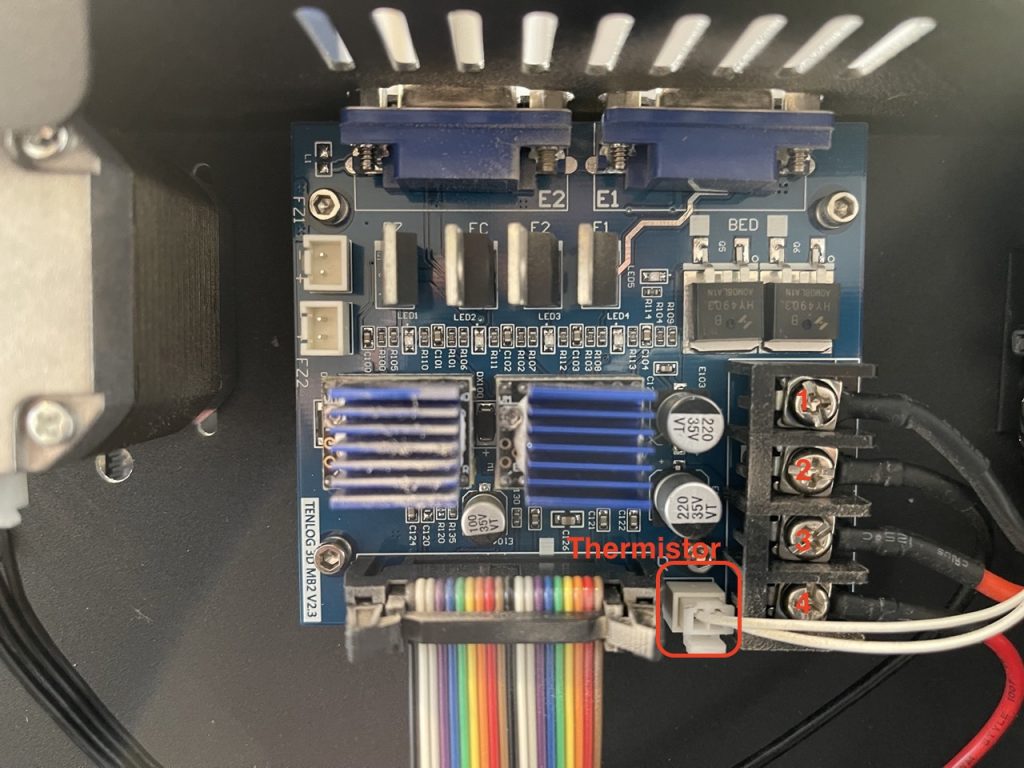
- Les bornes 1 et 3 vont au lit..
- 2 et 4 proviennent de l’alimentation.
Une Remarque : il est important de ne pas fixer le boîtier de relais tant qu’on n’a pas terminé le câblage, il faut accéder au dessous de celui-ci (pour la connexion à la terre)
La première connexion que j’ai faite était les câbles 1 et 3 aux relais 4 et 3 respectivement.
À ce stade, j’ai commencé à sertir certains terminaux pour faire les choses correctement.
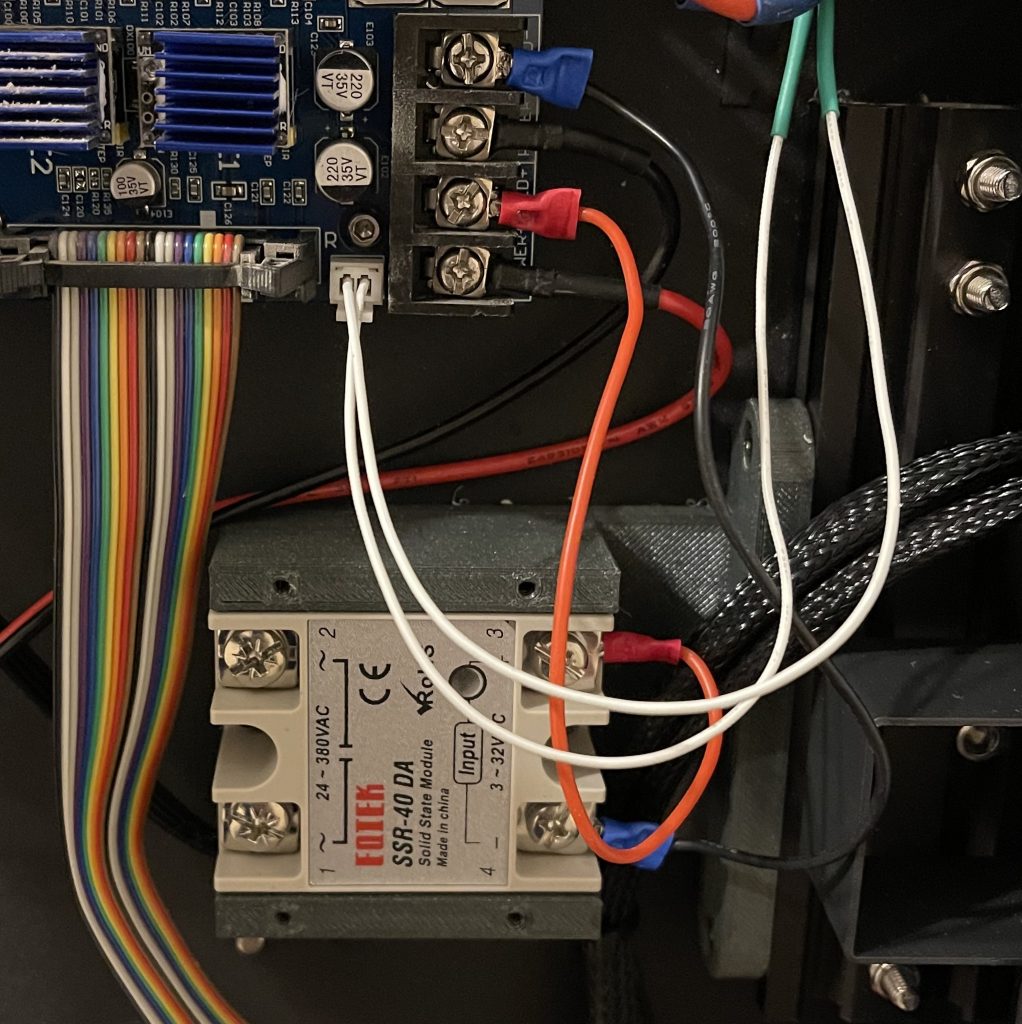
Pour la partie suivante, j’ai décidé de câbler la prise GX20 pour pouvoir retirer le lit plus tard.
J’ai utilisé le côté gauche pour la thermistance (la polarité n’est pas importante) et le côté droit pour l’alimentation (la polarité n’est pas importante mais je l’ai gardée cohérente dans le boîtier). C’est la partie dangereuse, j’ai ajouté une note autocollante avec le câblage juste pour être sûr de ne pas croiser les câbles, vous ne voulez pas que 220v aillent vers votre thermistance.
Vient ensuite le câblage du relais au bloc d’alimentation.
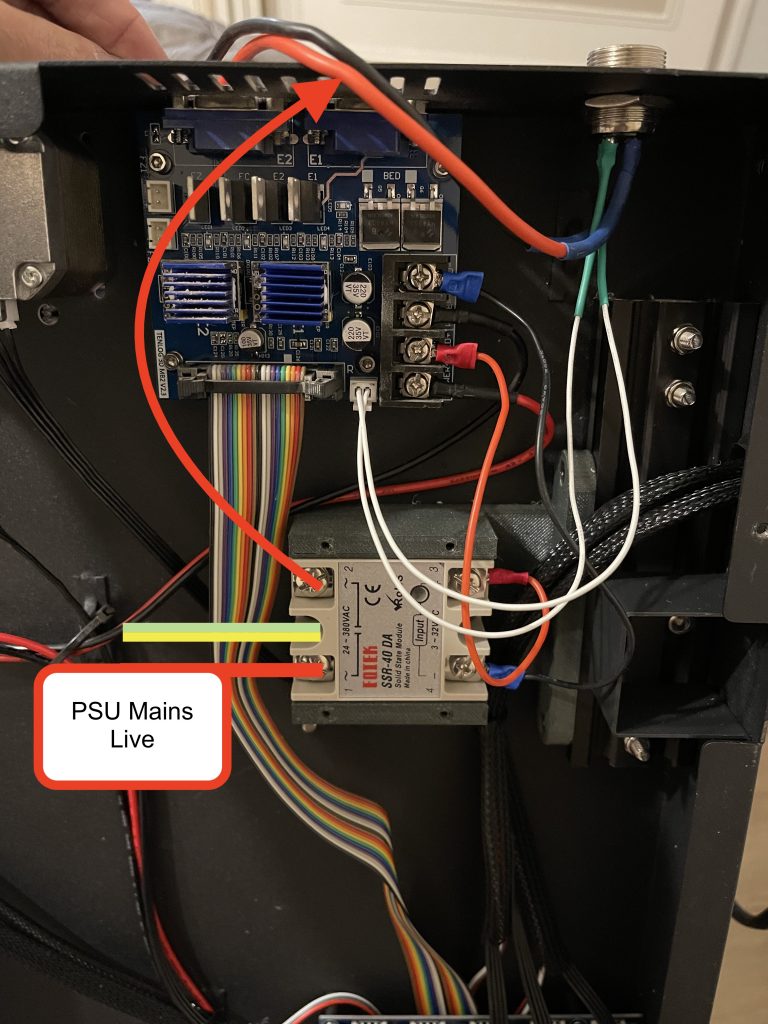
J’ai connecté la borne 1 au fil PSU Phase (P), j’ai interrompu ce câble avec un porte-fusible et y ai placé un fusible de la même valeur que l’imprimante utilise pour le PSU.
J’ai connecté la vis centrale du relais (qui maintient le relais au boîtier) à la masse (⏚) de l’alimentation. Borne 2 du relais au câble rouge sur le connecteur GX20 (la polarité n’a pas d’importance mais facilite l’interprétation du circuit lorsqu’on y travaille).
Le câble noir du connecteur GX20 va directement au Neutre sur l’entrée PSU (N).
À ce stade, j’ai fixé le relais au boîtier de maintien, le boîtier au profil X (à l’aide d’écrous en T) et le couvercle du boîtier de relais au boîtier (c’est TRÈS important, car ces bornes sont connectées à la tension secteur). J’ai ensuite fermé le boîtier et retourne la machine.
Avoir la prise GX20 me permet de gérer le câblage à l’extérieur sans me soucier de l’intérieur du boîtier.
À ce moment, le lit doit être détache, reportez-vous à la vidéo de TeachingTech d’en haut si vous voulez voir ce processus, mes mains étaient en quelque sorte pleines.
J’ai dû dessouder le câblage précédent, ce n’était pas une mince affaire puisque le lit est un dissipateur de chaleur. J’ai utilisé la plus grande pointe que j’avais, le fer très chaud et j’ai ajouté de la soudure pour faciliter le processus (j’ai besoin d’une station de dessoudage).
Le remplacement est alors juste un autocollant qui va sous le lit existant.
J’ai remplacé le lit et assemblé le mâle GX20 avec les fils existants.
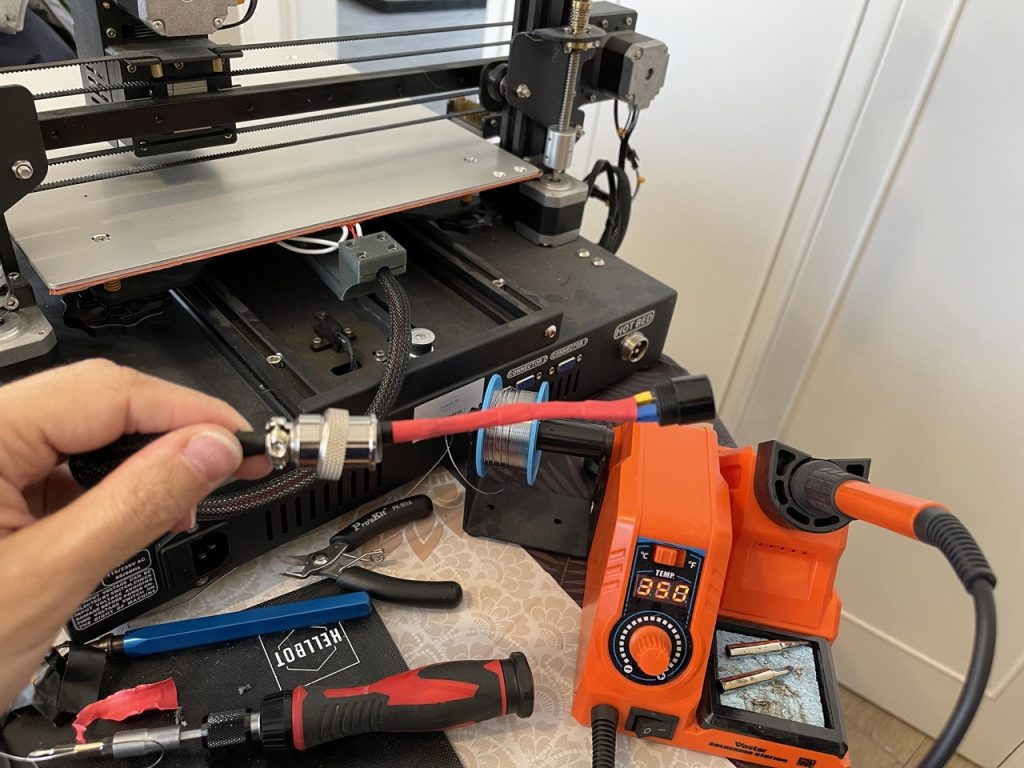
J’ai réutilisé le treillis de câble fourni avec l’original mais j’ai ajouté des quantités importantes de film rétractable pour l’isoler.
J’ai essayé d’utiliser la pièce fournie par StudioLab 39 pour gérer le câble (illustrée ci-dessus comme une pièce grise clipsant les câbles derrière le lit) mais elle ne correspondait pas à mon modèle. Il était lâche et empêchait également le mouvement du lit vers l’origine de Y. Je suppose que les pièces fournies fonctionnent mieux avec les modèles plus anciens ou avec la modification des rails linéaires du lit qui le soulève un peu.
Pour terminer le câblage, j’ai soudé le fusible thermique dans le câble et collé sous celui-ci avec du ruban polyimide.
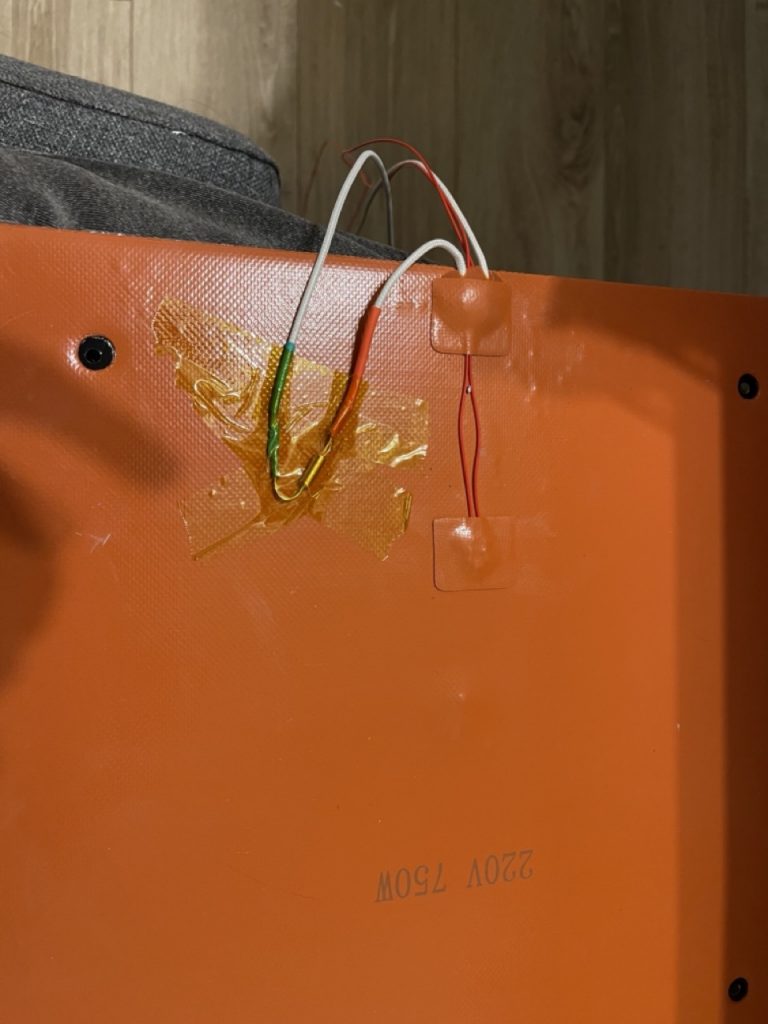
Il est important que rien de tout cela ne soit exposé car il est câblé à la phase. Ce fusible coupera l’alimentation si la température dépasse sa valeur nominale (j’en ai mis un pour 110C si je me souviens bien, je n’imprime rien qui justifie un lit plus chaud).
Après avoir terminé cela, j’ai juste rangé les câbles (j’ai utilisé du film rétractable car je n’avais pas d’attaches zip pour remplacer celles que j’ai coupées).
Côté firmware, la seule chose que j’avais à faire était d’exécuter un PID Auto-tune qui n’a pas fonctionné car Tenlog utilise une ancient version of marlin qui est fortement personnalisée.
Résultat final, ça marche, il y a un dépassement important lors de la chauffe mais une petite correction sur le slicer le compense (je me retrouve avec environ +5C de ce que j’ai demandé la plupart du temps)